International search engine for Technology for Meat and Alternative Proteins
Status: Exhibitors of IFFA 2025
VEMAG Maschinenbau GmbH
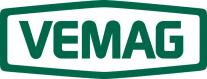
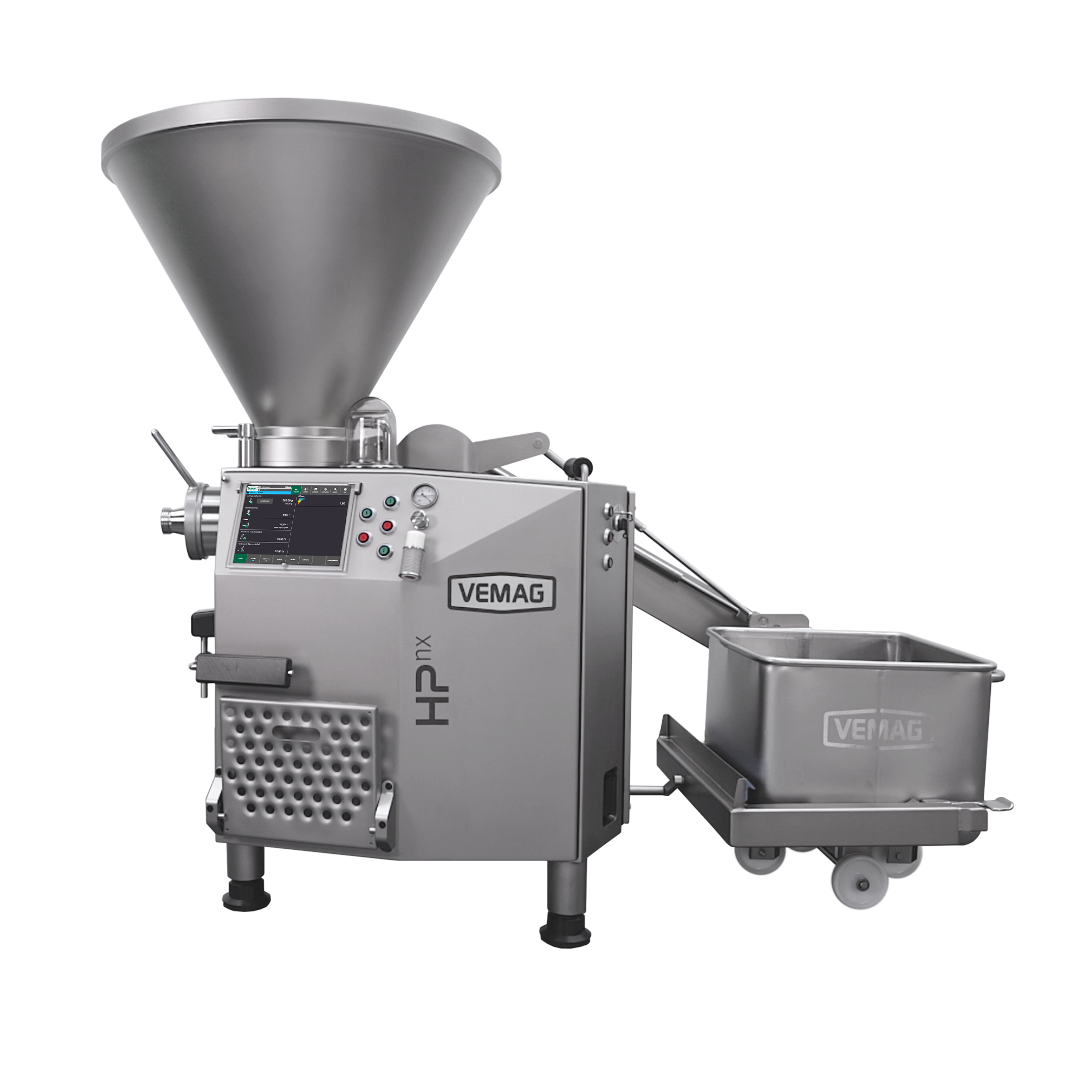
Die Vakuumfüllmaschine der nächsten Generation
Explore product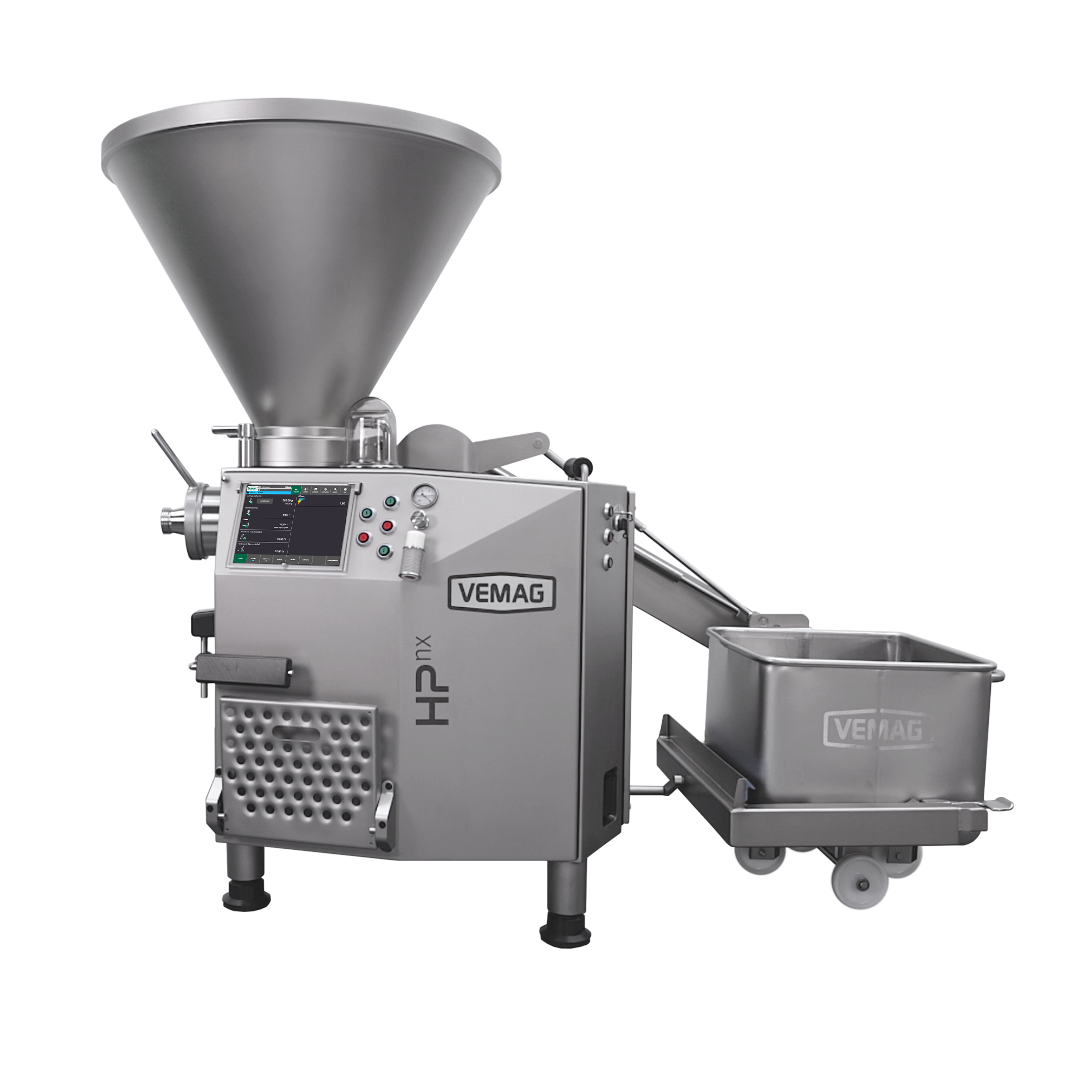
Die Vakuumfüllmaschine der nächsten Generation
Explore product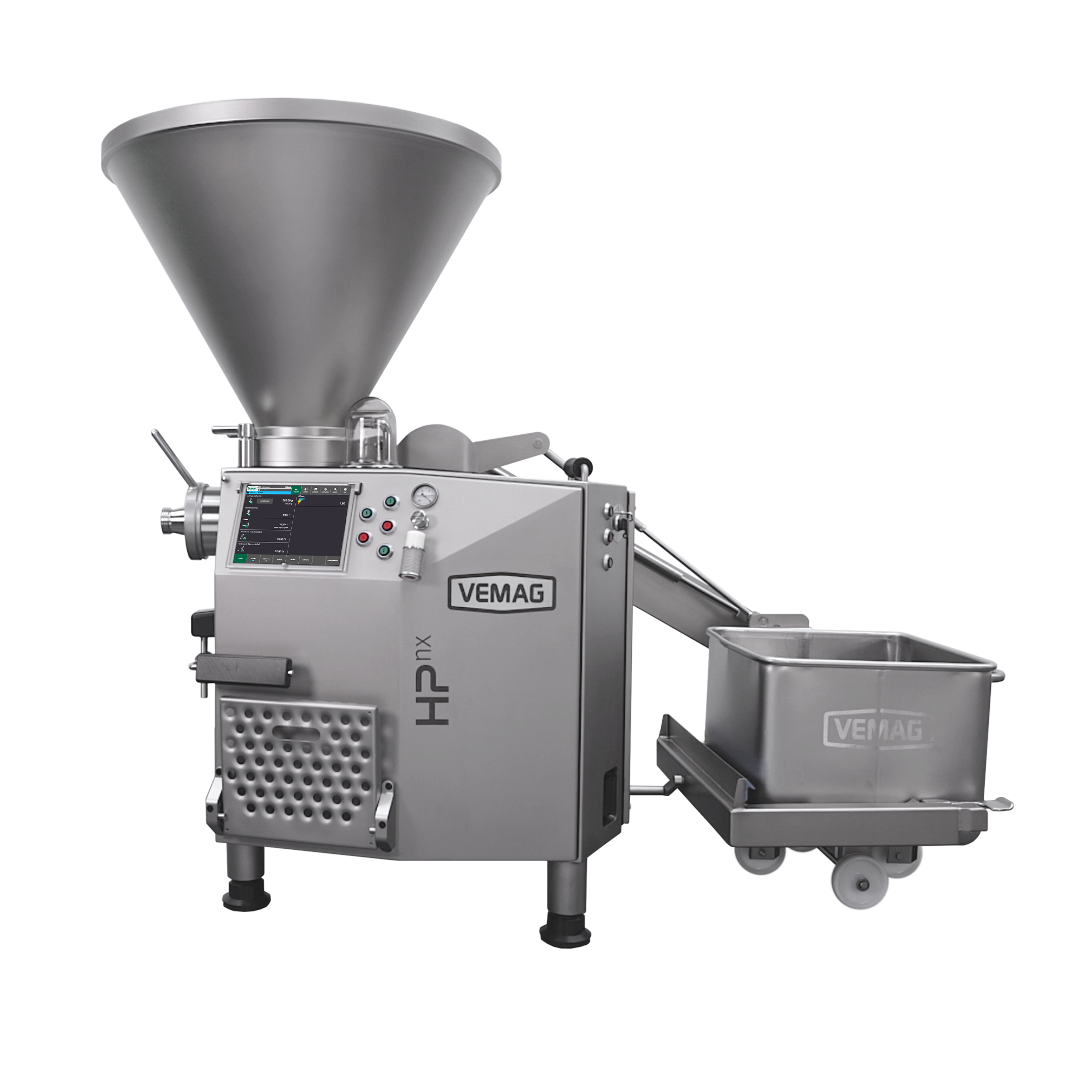
Die Vakuumfüllmaschine der nächsten Generation
Explore productAddress
VEMAG Maschinenbau GmbH
Weserstr. 32
27283 Verden (Aller)
Germany
Fax+49 4231 777241
Discover more from us
About us
With decades of experience and around 900 employees, we have been offering a comprehensive and innovative range of services for a constantly growing customer base. The basic concept is a modular system of standard fillers and customized attachments that can be flexibly tailored to the specific requirements of the user. The result? Efficient solutions that cover production capacities from small-scale to large-scale operations as well as all applications. Whether filling and portioning, grinding and forming, dividing doughs and masses, or innovative portion-to-pack solutions - everything is possible!
The company is led by the managing directors Andreas Bruns (chairman), Ralf Preuß (deputy chairman), Sven Köhler and Christoph Thelen. The company is active worldwide and achieves an export share of over 80 %.
We produce and manufacture exclusively at our site in Verden (Aller), Germany. The benefit of our customers in mind, we constantly pursue the goal of increasing efficiency in an inspiring and modern working environment. Together with our customers and representatives, we aim to flexibly and quickly understand the requirements of our markets, translate them into functions and machines, and further develop them for the benefit of our customers.
Our product groups
- Filling equipment (vacuum)
- Sausage twisting systems
- Sausage cutting and clip removal machines
- Complete systems for sausage and plant-based sausage production
- Other machinery for grinding, mixing, filling and sausage production
- Moulding equipment
- Wet extruders
- Ham/bacon filling and portioning machines
- Other maschinery for portioning, forming, extruding and treating
- Sorting and conveyor equipment for packaged goods
- Metering and portioning equipment
- Metering scales, belt scales
- Check weighing scales (including higher-load check scales)
- Process automation
- Operational data acquisition
- Production planning and control
- Other automation and handling equipment
- Casing spooling device
More about us
Special Interests
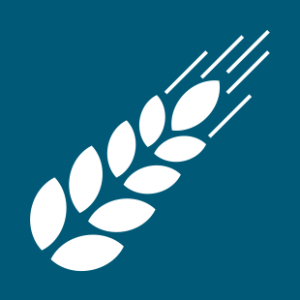
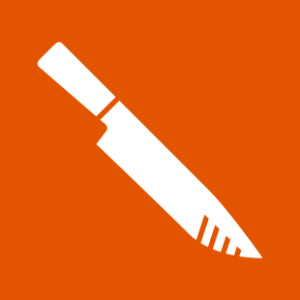
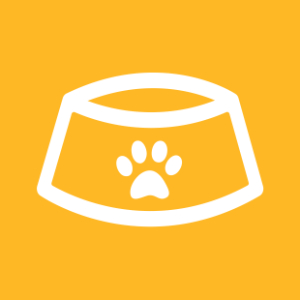
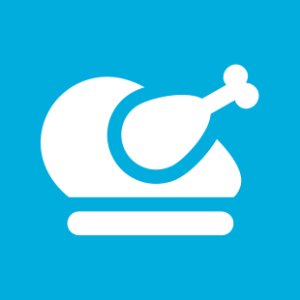
Keywords
- Förderkurve / double screw
- Automatisierung / Automation Custom
- Sonderkonstruktion / Custom made solution
- Portionieren / Portioning / Füllen / Filling
- Wolfen/ Grinding / Formen / Forming / Trennen / Cutting
Our Products
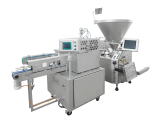
Convenience products - VEMAG brings forming, filling, portioning and packaging to a simple formula
Flexibility means a competitive advantage in the production of convenience products and with the machines from VEMAG Maschinenbau GmbH, Verden/Aller, Germany, the product portfolio can be expanded at any time. From savoury to sweet, meaty or vegetarian, filled or unfilled: The production possibilities are multifaceted. Always close to the market and the needs of the customers, the new developments are all about complete solutions. With its vacuum filling machines with proven double screw technology and a flexible, extensive range of attachments, VEMAG offers solutions for every requirement, making it possible to react at short notice to changing demands for a wide variety of products. According to the "modular principle", from which the user selects the building blocks he/she needs, VEMAG works with him/her to put together exactly the machine system that meets his/her needs and with which he/she can grow if he/she wants to manufacture new products economically and in first-class quality.
A wide range of products
For first-class shaped products with a perfect bite, such as meatballs, cevapcici, balls, köfte or even plant-based nuggets, the Ball Control BC236 comes into play: The BC236 is a universally applicable machine for the production of convenience products. These can be unfilled or filled. There are many applications for which the BC236 can be used. Minced meat balls, croquettes, cheese balls with filling, minced steak with feta cheese or vegetable balls with bechamel filling: The products can be spherical or drop-shaped, cylindrical or stepped, filled or unfilled, with a weight from 1 gram and a diameter between 10 and 60 mm depending on the variant.
The shaping of the products is realised by counter-rotating perforated plates, which are adapted to the product shape and through which the mass is guided. The high weight accuracy on all lanes is ensured by a filling flow divider, which divides the product flows evenly and thus provides an exactly defined quantity at all outlets. An optional flattening belt ensures a perfectly shaped patty - on up to six lanes.
Clean and accurate to weight
With the FKL609, VEMAG also offers the right solution for the automatic filling of cans, jars and cups. The system was built to fill pasty and liquid products into the packaging with portion accuracy. It operates at an average cycle rate of between 30 and 60 packages per minute. The FKL609 allows the use of different packaging sizes without time-consuming changeover work as well as the processing of various flowable products such as sauces, meat emulsion or stews - there are no limits to the range of applications for convenience products!
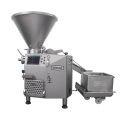
Die Vakuumfüllmaschine der nächsten Generation
Vakuumfüller der nächsten Generation
Die VEMAG Maschinenbau GmbH, Verden/Aller, präsentiert eine neue Vakuumfüller-Generation – die HPnx. Es ist die konsequente Weiterentwicklung der am Markt etablierten HPE-Serie. Mit dem neuen Vakuumfüller lassen sich unterschiedlichste Massen, pastöse Lebensmittel und andere Rohstoffe schonend und gewichtsgenau portionieren. Zahlreiche Optimierungen sorgen für eine hohe Produktqualität, minimale Restmengen und eine höhere Maschinenverfügbarkeit. Gleichzeitig sinken die Betriebskosten. Zudem setzt die neue HPnx in Punkto Flexibilität, Bedienbarkeit, Sicherheit, Leistung und Hygiene neue Maßstäbe.
Förderkurventechnologie
Bei der HPnx setzt VEMAG auf die Förderkurventechnologie. Damit wird das Produkt besonders schonend verarbeitet. Die Gewichte sind beim Portionieren sehr exakt. Das zuverlässige „First In – First Out-Prinzip“ der Förderkurven gewährleistet Sicherheit in der Produktion, denn der gerade und direkte Produktstrom verhindert Toträume und Transportverluste. Die wenigen Bauteile, bestehend aus Förderkurve und Förderkurvengehäuse, lassen sich einfach und schnell zusammen- und auseinanderbauen. Das ermöglicht eine optimale Reinigung. Zudem gewährleisten die langlebigen und hochresistenten Bauteile für eine hohe Maschinenverfügbarkeit und geringe Kosten. Und das Wichtigste: das Förderwerk sorgt für ein luftfreies, gewichtsgenaues und sehr schonendes Füllen. Dies bedeutet auch eine Erhöhung der Produktionseffizienz und weniger Give-Away.
Neuer Hygienestandard
as die Hygienestandards betrifft, haben die Experten aus Niedersachsen die Füllmaschine weiterentwickelt, optimiert und auf ein neues Level gehoben. Eine Neuheit: der Vakuumkanal bei der HPnx ist nun spülbar. Eine Reinigung des Systems ist einfach und schnell möglich. Der Wasserablauf im Maschinenfundament garantiert, dass der Vakuumfüller nach der Reinigung unverzüglich wieder in Betrieb genommen werden kann, da das Wasser ungehindert abläuft. Generell ist die Maschine so konstruiert, dass das Wasser insgesamt noch besser ablaufen kann. Vorteilhaft ist außerdem, dass sämtliche Bauteile gut zugänglich sind.
Der optionale Reinigungstisch, der am Auslass der Maschine montiert ist, ermöglicht die sichere Verwahrung aller Bauteile während der Reinigung. Nach dem Ausbau der Förderkurve und des Förderkurvengehäuses können diese einfach auf dem Reinigungstisch abgelegt werden. Nach der Reinigung der Maschine können die Bauteile schnell wieder montiert und die Produktion wieder aufgenommen werden. Alle Teile sind jederzeit griffbereit, was zu einer noch effizienteren Produktion beiträgt.
Service und Wartung
Die gesamte Steuerelektronik liegt innerhalb der Maschine in einem dampf- und staubdichten Gehäuse aus Edelstahl. VEMAG bezeichnet diese bewährte Konstruktion als „Box-in-Box“. Zu erreichen ist der gut geschützte Elektronikbereich über große Schwenktüren, welche den Zugang erleichtern.
Ein separater Altfettbehälter, die neue Kabelführung und das Box-in-Box-System sorgen insgesamt dafür, dass der Innenraum der Maschine sehr aufgeräumt und übersichtlich ist.
Auch die Bodengruppe der HPnx wurde optimiert. Eine verstärkte, durchgehende Bodenplatte im Maschinenfundament sorgt dafür, dass sich die Maschine bei Bedarf einfach und sicher transportieren lässt.
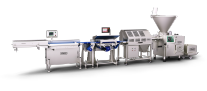
Safe production of minced and shaped products
Loose, juicy, with an appetising appearance, delicious taste, convincing mouthfeel and pleasant bite - just like homemade. This is how consumers want their fresh meat product. The technology of VEMAG Maschinenbau GmbH, Verden/Aller, Germany, guarantees premium quality and optimises existing production processes. From the classic minced meat portion to burger patties to shaped specialities such as cevapcici or meatballs - with filling systems and filling grinders for continuous separation as well as attachments for shaping the end products and depositing the food in the packaging, VEMAG offers highly productive automation solutions for the weight-accurate production of different, dimensionally stable products.
Efficiency and precision already start with the filling of the vacuum filling machines. By means of the VEMAG DuoDrive, the product is gently transported into the double screw via a hopper. This results in a uniform filling flow for perfect further processing, because there is no back pressure during the grinding and separation processes and the product does not heat up during processing. Directly driven by the double screw of the filling machine, the separation grinder982, for example, gently grinds the raw material to the desired final grain size. This guarantees uniform granulation, excellent colouring, particle alignment and a clear structure for the desired product appearance. During the grinding process, heat generation is avoided and the large diameter of the grinder prevents pressure build-up and thus changes in the product texture. The integrated separator, e.g. the 813, continuously removes unwanted particles during processing and ejects them safely. This ensures premium products of the highest quality. At the same time, the handling and cleaning of the system is particularly easy.
Burger patties as if made by hand
In further processing, for example, the FM250 shaping machine is the reference for industrial burger production, with the bite, texture and appearance of a premium-quality handmade patty. On the one hand, the FM250 forms so compactly that the end product holds together well during preparation, while on the other hand it remains fluffy with a juicy, soft texture. The FM250 achieves this by gently conveying the raw material so that the meat fibres remain intact and maintain an even alignment. A flattening belt brings the products running on a conveyor belt to the desired final size. The patties are then automatically placed in trays, for example. The VEMAG FM250 forms up to 300 portions per minute.
At IFFA 2025, VEMAG will be exhibiting numerous other solutions for the production of fresh meat products, including the Paper Interleaver PI355 for automatic positioning of paper or film under the individual portion and the Automatic Meatball Loader AML273 for weight-accurate production and fully automatic depositing of meatballs or cevapcici in trays.
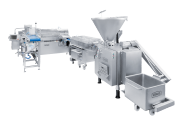
Intelligent automation solutions from a single source
VEMAG Maschinenbau GmbH, Verden/Aller, Germany, will be presenting numerous innovations on the subject of automation at IFFA 2025. Under the motto "Boundless Product Passion", the solutions increase product safety on the one hand and reduce personnel costs on the other. At the same time, the focus always remains on the product and its high quality. At the trade fair, the specialists from northern Germany will present high-performance machines that continuously portion, fill, shape, process, group and place various products in a wide variety of packaging with gram accuracy.
Trade fair visitors can expect a range of highly flexible and user-friendly automation solutions for filling, portioning, shaping and depositing in the packaging. Whether minced meat, burgers, vegan and vegetarian products, sausages or convenience products - there are no limits to the range of applications. The fully automated depositing and packing can take place, for example, in cups, jars, trays, cans, thermoformers, flow wrappers or other packaging. A wide variety of further packaging lines can be fed. The VEMAG Multiloader and shuttle conveyors, for example, discharge single-lane portioned products in multiple lanes in the transport direction of the packaging machine and allow different product groupings when depositing in trays/thermoformers: side by side, shingled or stacked.
Grouping sausages
The VEMAG Linkloader LL335 is a complete, universally applicable grouping system for fresh sausages, which are placed fully automatically in groups in trays and passed on to the downstream process. The Linkloader LL335 fully automates the previously labour-intensive process of grouping and loading sausages. The avoidance of manual labour as well as the depositing without accumulating effectively prevent pressure marks on the sausages as they can occur through touching. By eliminating manual labour, a new dimension in hygiene standards is achieved. With a speed of up to 40 trays/minute for natural casing applications and up to 600 portions per minute for collagen casing and alginate casing applications, depending on portion size, the LL335 accurately places sausages. Defective portions as well as the first and last sausage are reliably sorted out so that only faultless products are processed further. This increases the quality of the sausages and the packable quantity with the same raw material input.
Absolute weight accuracy
Product safety and absolute weight accuracy play just as important a role as flexibility in the use of a wide variety of packaging formats, packaging materials and fast changeover times. In production, it is ultimately important to fill containers and packaging precisely, quickly, accurately and reliably.
In addition, with the Link Grouper 336, VEMAG offers options for automatic and efficient loading of, for example, oven or freezer belts with sausages in alginate casings, collagen - and natural casings.
VEMAG offers the right solution from a single source: Together with a VEMAG vacuum filling machine, all attachments for portioning, filling, shaping and placing into packaging form a complete solution. Whether pasty, flowable or chunky - the volume-based filling quantities are identical, all products are filled with weight accuracy and gently, thus offering intelligent automation solutions from a single source.
VEMAG's flexible automation solutions are ideally complemented by the digital solutions of the further developed Smart Link, which enables permanent production data acquisition, evaluation and optimisation and thus planning at a glance. Even integration into ERP systems is no problem via the available OPC/UA interfaces. The company thus offers intelligent solutions from a single source "Made in Verden".
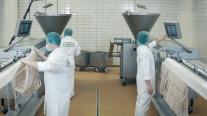
Sausage production with VEMAG: performance, precision, weight accuracy, flexibility and reliability
In order to master the versatile tasks of sausage production, it is important to use production technology that offers great flexibility and almost unlimited expansion possibilities. The product variety that can be covered by the sausage lines of VEMAG Maschinenbau GmbH, Verden/Aller, Germany, is almost inexhaustible. Simple adjustment and re-fitting work turn production lines into all-rounders. With a flexible and modular range of machines and attachments, users can expand their product portfolio at any time. Filling, grinding, separating, applying and changing casings, portioning and linking, separating, depositing or hanging: From Wieners to raw sausage snack products and sausages in alginate casings, the mechanical engineering company from northern Germany offers everything from a single source "Made in Verden".
Uniform product appearance
Same length, same weight, same calibre: VEMAG machines for linking achieve a particularly high reproducibility of results for a uniform product appearance and maximum weight accuracy - regardless of which casing is being processed. The length portioning device LPG218 and the identical and mirrored LPG238 offer exactly that: The unique VEMAG gripper principle ensures that the casings are perfectly positioned on to the linking horn and stabilises them during loading. This prevents misloading and buckling of the casings. An integrated casing feeder additionally supports the linking function and ensures that the casing is gently and consistently advanced. Precisely linked sausages, efficiency and automation are the clear focus.
An additional challenge is the changing demands of the market: the demand for cost-saving and more environmentally friendly solutions that are also suitable for the production of vegetarian and vegan products is increasing. The use of alginate, a natural gel made from brown algae, which is used as a sausage casing, is becoming increasingly popular. The VEMAG CC215 attachment is used, for example, to evenly coat the sausage meat or product portioned by the vacuum filler with alginate. The high accuracy of the layer thickness guarantees reproducible quality and low material costs. Immediately after leaving the coextrusion head of the CC215, the gel-like alginate is sprayed with a calcium chloride solution and hardens directly. The sausage meat or product strand prepared in this way is now processed further according to the customer's wishes: directly onto a hanging line, e.g. for salami snacks, individually onto a belt or prepared for a thermal process. Direct depositing in trays is also possible.
Depositing and grouping
The solutions for grouping and depositing sausages are equally convincing. With the LinkLoader LL335, for example, separated fresh sausages are automatically deposited in groups in trays and passed on to the downstream process. Avoiding manual intervention and depositing without accumulating prevents pressure marks on the products that can result from touching. The elimination of manual activity also adds a new dimension to the standard of hygiene. The previously labour-intensive process of aligning and grouping sausages is fully automated by the Linkloader LL335. At a speed of up to 600 portions per minute, depending on the portion size, the LL335 accurately places sausages in collagen casings or with alginate casings. Defective portions as well as the first and last sausage are reliably sorted out so that only perfect products are processed further. This increases the quality of the sausages and the packable quantity with the same raw material input.
VEMAG offers process solutions for the sausage sector from filling to depositing from a single source. The solutions promise a high degree of automation with maximum efficiency and hygiene. Manual work and give-away are reliably reduced - for precise, weight-accurate, flexible and reliable sausage production.