International search engine for Technology for Meat and Alternative Proteins
Status: Exhibitors of IFFA 2025
Fava Giorgio Axel s.r.l.
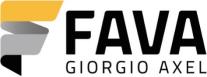
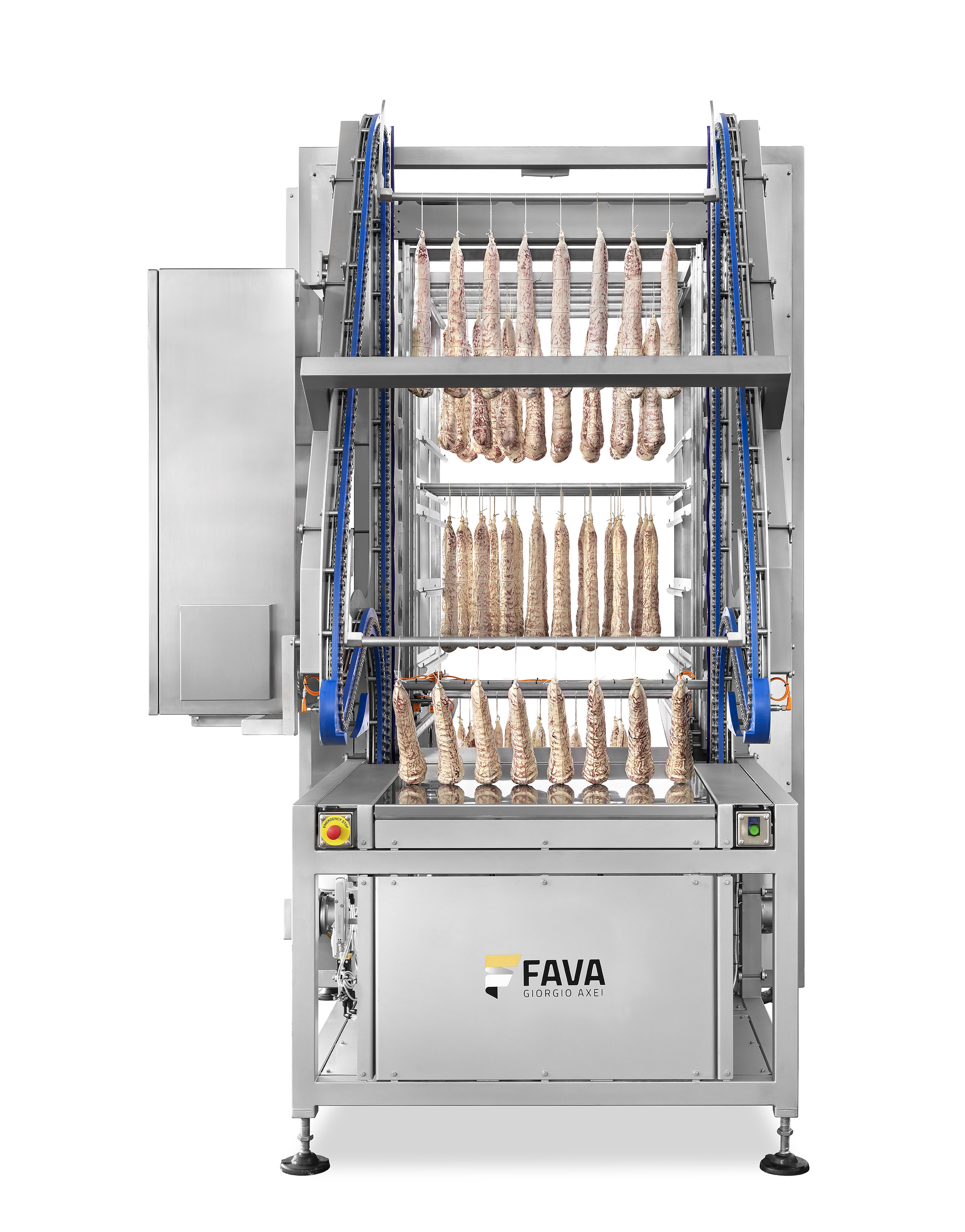
LOADING AND UNLOADING SYSTEM FOR SALAMI
Explore product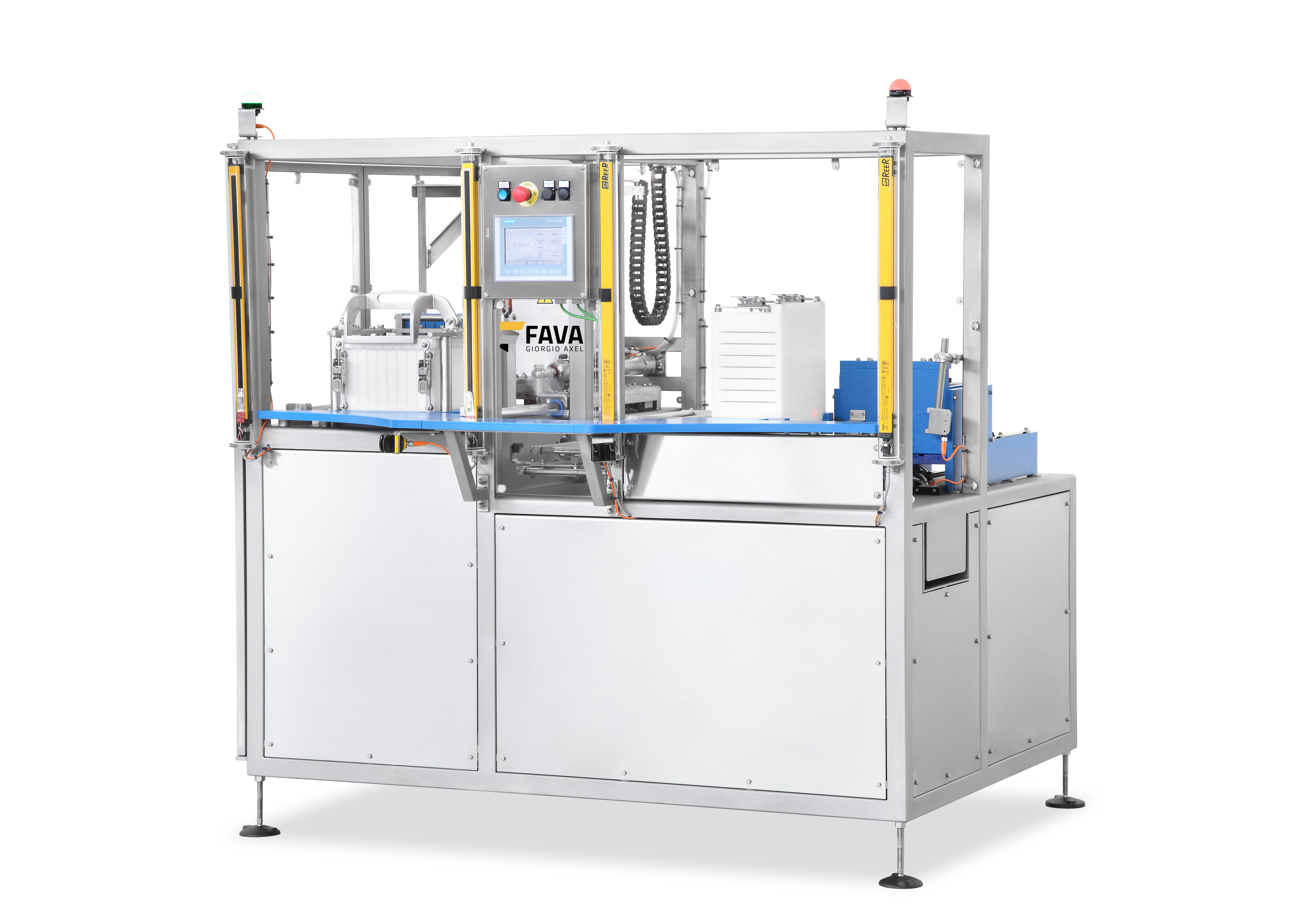
AUTOMATIC SKEWERING MACHINES
Explore product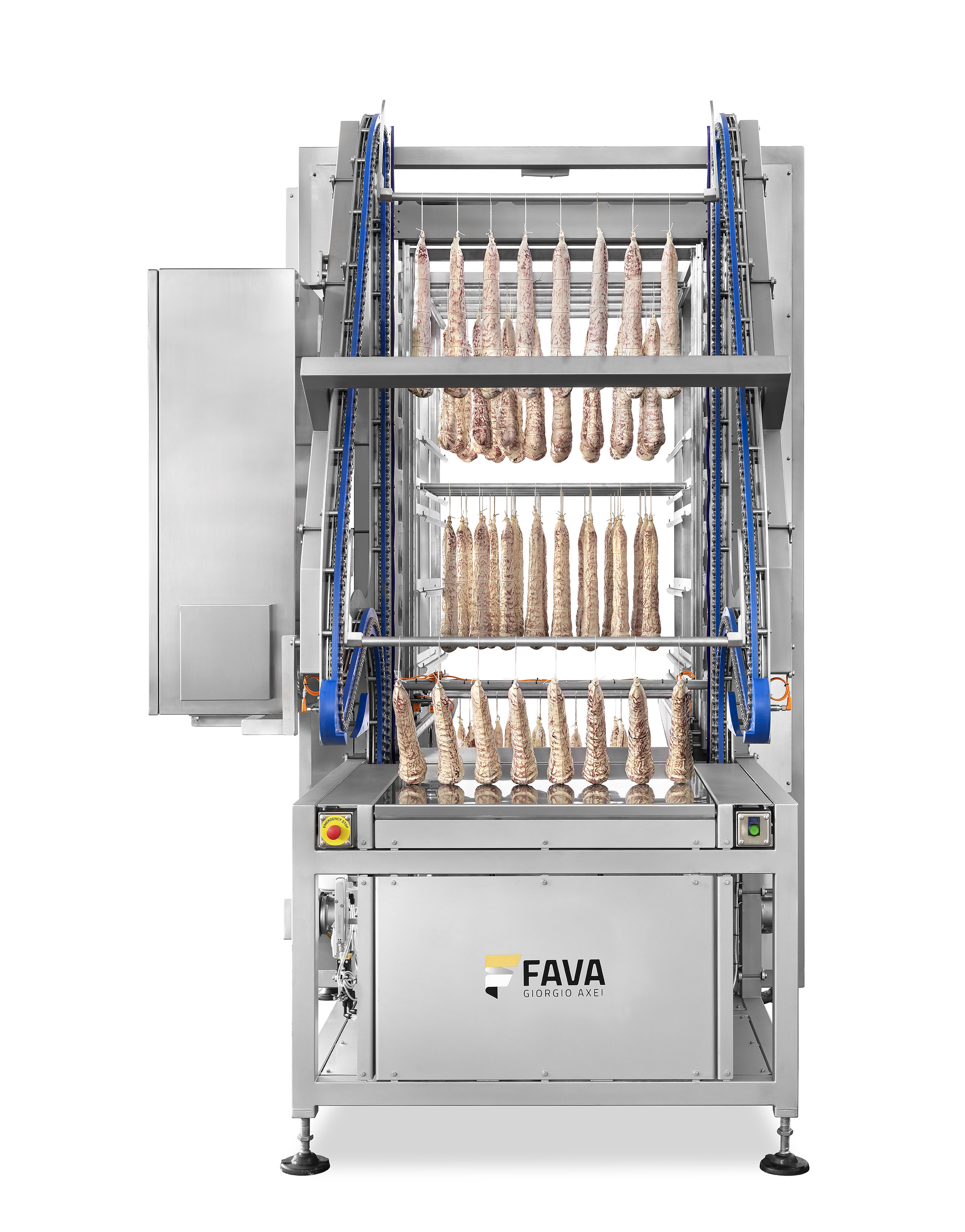
LOADING AND UNLOADING SYSTEM FOR SALAMI
Explore product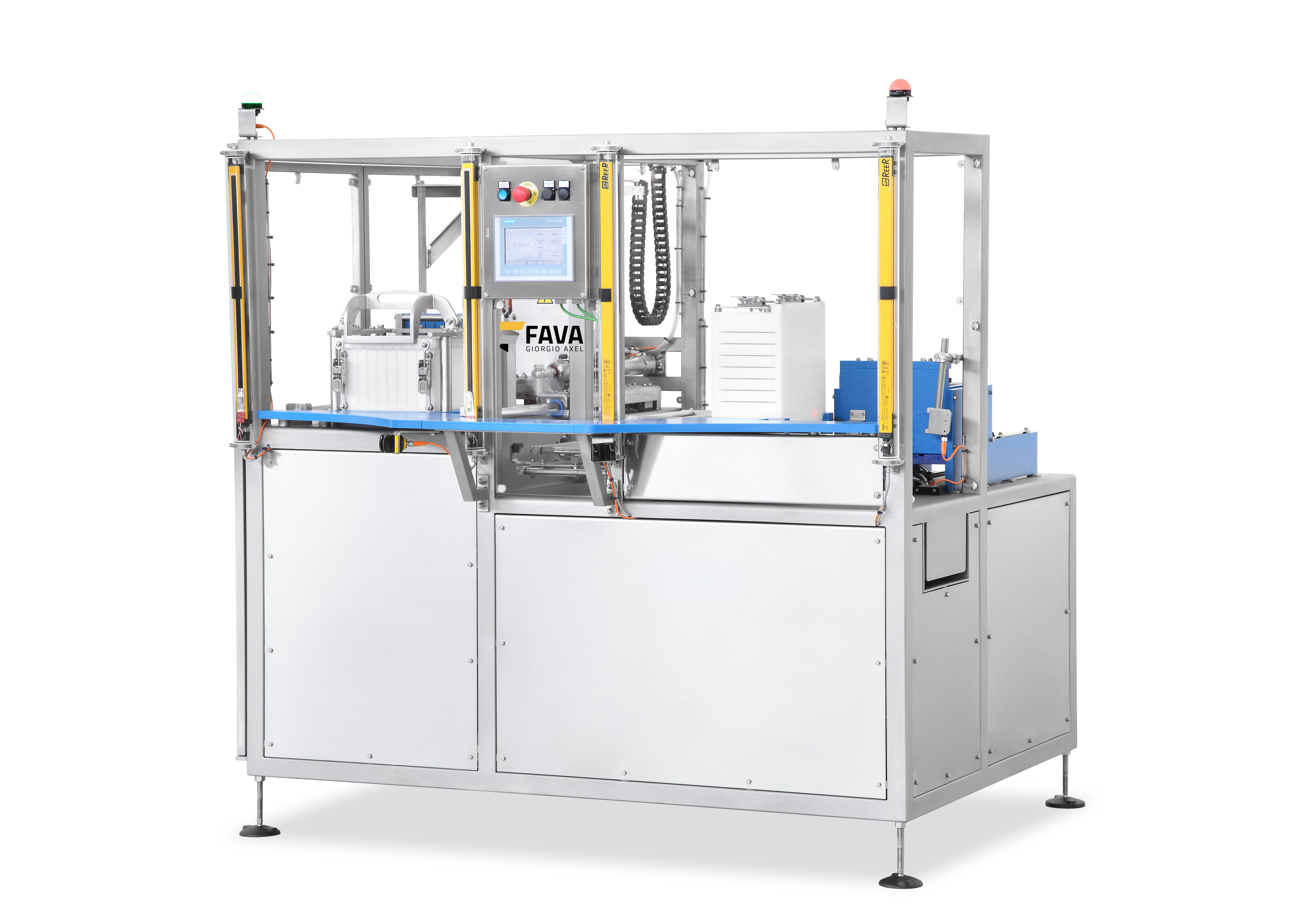
AUTOMATIC SKEWERING MACHINES
Explore product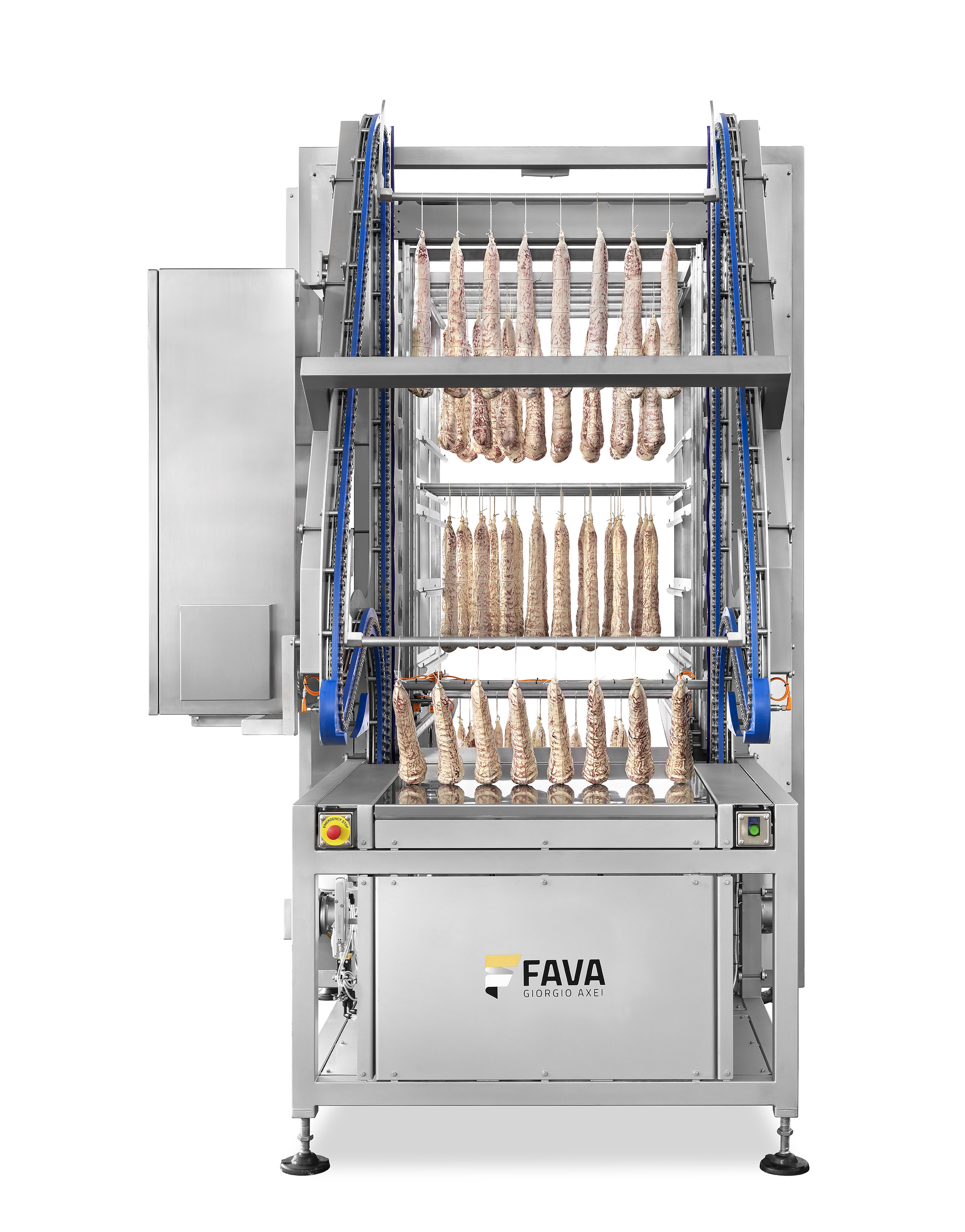
LOADING AND UNLOADING SYSTEM FOR SALAMI
Explore product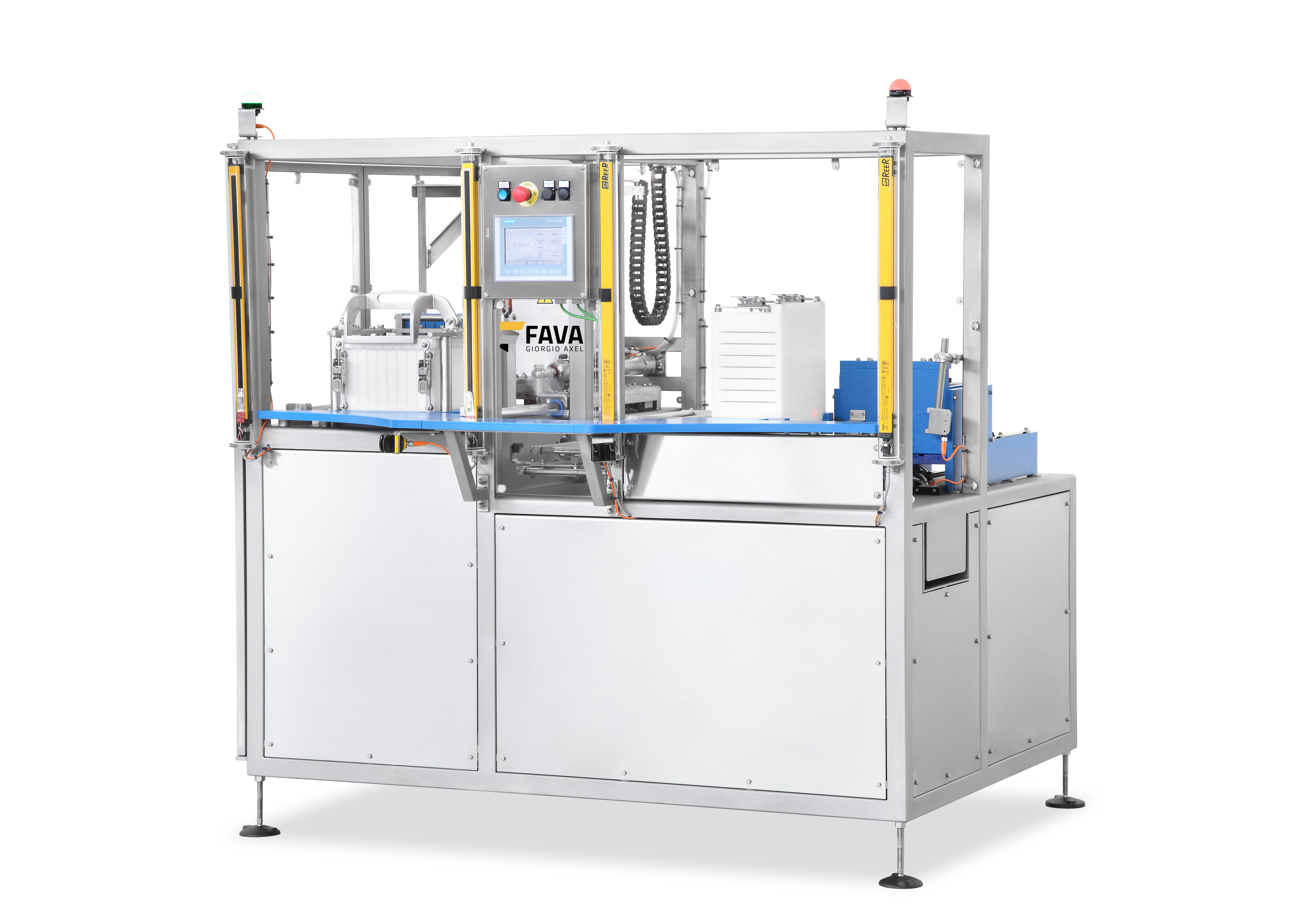
AUTOMATIC SKEWERING MACHINES
Explore productAddress
Fava Giorgio Axel s.r.l.
Via A. Cerati 19 A
43126 Parma
Italy
Telephone+39 0521 293734
Fax+39 0521 293968
Discover more from us
About us
Fava Giorgio Axel started in 1976 to produce machines for meat products processing factories, but it already had years of experience in the mechanical field even making machines and overhead rails sold by other companies. Gradually we extended our offer to other food industry sectors from cheese to sweets, from meat to fish.
Health, safety and life quality are the linchpins of our company, but also the inspiration of each project we realize.
The customer and his needs are the center of our company. Our machines have been created, one after the other, on our customers’ requests, to solve different kinds of problems as peak of production, versatility, products standardization, economies of scale.
Needs analysis is always our starting point and every time the challenge is putting together innovation and customization to find the best solution for the buyer, because each company is different in space, logistics, organization. The customer’s particular needs give rise to each single project.
Workers’ safety, sanitize, ergonomics and energy-saving are our priorities.
We pay a lot of attention to innovations and we constantly improve our products, even thanks to important partnerships.
More about us
Special Interests
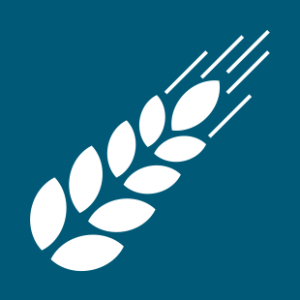
Keywords
- SALAMI UNLOADING
- LABELLING
- BACON COMBING AND DECOMBING
- AUTOMATIC LOADING AND UNLOADING SYSTEMS
- ROBOTIZED PACKAGING
- PORTIONING
- SKEWERING
- DECLIPPING AND CUTTING
- SALAMI LOADING
- PACKAGING
Our Products
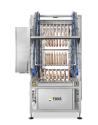
LOADING AND UNLOADING SYSTEM FOR SALAMI
The TFRC system for loading and unloading hung deli meats, on trolleys, frames, trees or suspended conveyors, even of great height, can handle different products at the same time, coming from semi-automatic loaders, from automatic loaders, or taken from frames from production areas where manual loading is limited to the easiest level.
The same system is part of our system for the automatic hooking and unhooking of bellies for bacon.It is possible to pick up all the bars of an entire level; optimal acceleration management allows high speeds with very little oscillation of the products, with high throughput without products dropping.
It is able to handle frames of great height and handled by AGVs and of suspended tray conveyors. When unloading, it is also possible to transfer one pole at a time to the packing or peeling lines, even with automatic bar extraction or loop cutting.
The special design mode, protected by international patents,reduces the cross-sectional footprint of the system (only 300 mm more than the length of the frames to be loaded or unloaded); it is the most compact and easiest system to fit into existing production facilities.
The compact loaders and unloaders for frames, trolleys, trees or suspended conveyors on which to place bars with hanging products can be fed either by manual product placement stations on the bars, by automatic loading devices for salami or other products on bars. We also offer a version that can be used both as a loader and an unloader. The design, derived from our TFRC loading system, allows customizations depending on the length of the hanging bars (poles), the size of the frames (or trolleys or tees or suspended tray conveyors), and the size of the products. In the case of semiautomatic loading, the insertion of the hanging bars into the loops is manual as is the effortless positioning into the hooks of the lifting catenary for subsequent storage in the programmed level. It is also possible to feed the loader with automatic salamis hanging machines to the bars.
All models move the arms that deposit the bars with the hanging cold cuts vertically, to adapt to the frames, which, with the same width, can have different heights and lengths, just as the heights of the levels to be loaded can be different, also depending on the product.
The compact loader, like the unloader, makes it possible to proceed with the formation of levels even while replacing a full frame with an empty one, of course in total safety.
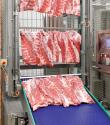
Bacon handling: combing and loading – unloading and decombing
The system for combing and loading bellies includes conveyor belts that feed the insertion units into the bars, a dynamic store from which the empty bars are taken, another for the bars with the product combed, and a TFRC Cartesian robot for frames or trees that transfers the empty bars into the dynamic store and picks up the bars with the bellies hung to load them into the frames, or trees, as soon as they are emptied. The system can process up to 8 bars/1′, with bellies from one or two feed lines, thus up to 40 bellies/1′ and the hooking device can load continuous systems.
The system for unloading and extracting the bars from the bellies includes a TFRC unloading unit that transfers the bars with hung, cooled or frozen product to a dynamic storage unit, and then picks up the empty bars and loads them orderly into the frames, or trees, to be transferred to the washing machine. The de-combing device extracts the bellies to transfer them to downstream processing stations; maximum throughput is 40 bellies/1′, also for the unloading of bellies from continuous systems.
Benefits
- Reduced manpower in the combing, de-combing and washing areas
- Reduction in management stress due to workers not showing up for work
- Reduction in employee turnover
- Reduction in strenuous and repetitive work
- Reduction in occupational injuries and illnesses
- Increased yields with better quality bacon
- Improved yields through controlled mechanical combing and hanging
- Elimination of overlapping and missed catching of CT muscle.
Key features
- RELIABILITY: systems developed on simple concepts, intrinsically strong and reliable
- ADAPTABILITY: no need to replace suspended conveyors, cooking and smoking systems, cooling units, perhaps not even frames, racks and trees
- COMPACTNESS: the least bulky on the market, it fits into most existing bacon processing plants
- FLEXIBILITY: can work with products having different dimensional characteristics, even simultaneously
- VERSATILITY: combing and extraction systems also suitable for continuous systems
- SOLIDITY: the hooked bars and trees/frames are designed to avoid mechanical stress, eliminating the costly breakage and replacement expense of combs and trees, with obvious reduction of maintenance costs
- SANITIZATION: easier washing and cleaning due to the improved design of hooked bars and trees
- POWER: one unit can feed 6 slicing lines producing up to 3 different products at the same time
- DESIGN: the system is specifically designed to also be used within existing bacon production units, can be easily adapted to production needs and expanded as the business grows.
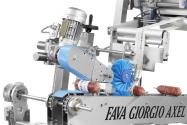
LABELLING MACHINE ETIFLEX
Automatic labelling machine for salamis Etiflex, pneumatic working and control, made of stainless steel and of plastic material for food contact.
The machine structure permits the operator to properly and easily position the product, while the un-loading can be done directly on a transferring belt to the downstream working areas or it can be done by an operator.
The machine is able to use adhesive, or partially adhesive, labels from 30 mm to 280 mm wide, depending on the model. With simple adjustments it performs the labeling of products with a diameter between 30 and 110 mm, and from 150 mm to 600 mm long. The productivity can reach 2.400 pieces per hour depending on the products’ diameter, consequently on the labels’ dimensions and on the operator loading speed. It is also possible to label flat products and U shape products.
The Etiflex labelling machine can be equipped with pigment transfer or ink-jet markers, and can print in plain text and in barcode, data such as production date, batch number, or whatever else is needed.
The label design and precision of the machine allow printing in a defined area, avoiding covering the company brand or other information.
The marker can also print data such as product name and ingredients, in the language of the destination country, eliminating the label changeover time and greatly reducing the label stock.
Our proposal also includes the Etiflex-W model, which can carry out the weighing of each single product, printing the weight, but also the price, in clear and with barcode, in a predefined area, without the need to add labels, without overlapping. The weighing system is certified.All Etiflex labelling machines can be equipped with a device for remote internet connection, both for technical assistance and for modifying the operating modes. Parameters can be stored in recipes, with indications from the operator panel that guide manual adjustment of parts such as the position of the labeling head, gate, brushes and winding belt.
It is possible to insert the machines in the production process for batch management and product traceability.
The touch screen operator panel can provide information, for example, on the type of label to be used.
AUTOMATIC PACKAGING
We produce different systems to package your products.
Our extremely compact CONFSV vacuum bagging and packaging lines can use either aluminum bags, shrink bags or taped bags. Easy adjustments ensure excellent qualitative and quantitative results and the different models can produce from 360 to 720 pieces/hour. They are used for cooked or cured products, whole or in portions, for cheese and for vegetarian or vegan products.The automatic bagging machine receives the products, appropriately oriented, on its loading conveyor belt. The gusseted bags or the sacks, are stacked in a special adjustable warehouse, orientable, or with a double drawer to allow loading without stopping production, for greater productivity. The packaging machine feeds our vacuum thermosealing tunnel, with sealing bars of 1.4 m, 1.8 m and 1.95 m, with side-by-side resistances conformed in such a way as to ensure maximum sealing pressure which, in this way, is less sensitive to micro-folds and the presence of traces of product.For bagging, a special device makes it possible to give to the mouth the shape required for the best and most reliable vacuum sealing, without the need for personnel. This device can be adjusted according to the size of the product.
CONF AUTOMATIC PACKAGING
The packaging machine for taped bags can also handle cylindrical-shaped products; like the previous ones, it is equipped with an infeed conveyor belt, a pusher and a spreading device which, in cooperation with a blower, allows the bag to be opened, minimizing the size of the bag with respect to the product. Our packaging machines can also feed vacuum belt machines of other manufacturers.
ROBOTIZED PACKAGING
We produce robotic systems for packaging in taped bags and automatic loading of the vacuum machine belt, suitable for circular and flat shaped products, be they mortadella or cheese or vegan and vegetarian products, with lengths up to 1.200 mm. The special design of the grippers makes it possible both to reduce the use of plastic material and to conform the mouth of the bags for better and more reliable vacuum sealing.
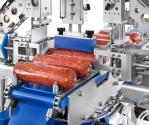
CLIP REMOVING AND CUTTING MACHINE
We produce two different models of declipping and cutting machines.
TDSAL automatic machine for clip removing and / or cutting in half, 45° or 90° angle, for cooked and cured products with 2 declipping heads and 1 cutting station and TTDDSAL with 4 declipping heads and 2 cutting stations.
A loading conveyor, working in step and controlled by a brushless motor, allows the precise positioning of the products in the clip removing station.The two de-clipping heads lean against the product, centering it transversally and acting in order to optimize the aesthetic result after the removal of the clips, with the least possible product removal.The products are then transferred to the cutting device, which divides them into two parts of approximately equal length and/or equal weight, depending on the characteristics of the product, and transfers them onto a conveyor belt, which can be customized, for transfer to subsequent processes.
The clip removing heads and the cutting unit are equipped with easily replaceable parts to adapt to the size of the products and to obtain the desired result even with partially retracted clips.
Product's dimensions vary from 30mm to 100mm in diameter and from 170mm to 600mm in length, depending on machine configuration. Productivity ranges from 15 to 17 pcs/1'.
TTDDSAL model is able to process up to 30 pcs/1’
An operator touch screen panel allows the management of the various types of machines and it provides operators with the necessary information, from use to maintenance. The machine's PLC allows both the connection with the company's management software, for production programming and product traceability, and the remote connection with our technical assistance service.
Our Contact Persons
Lorenzo Vettore
Sales
Project Manager
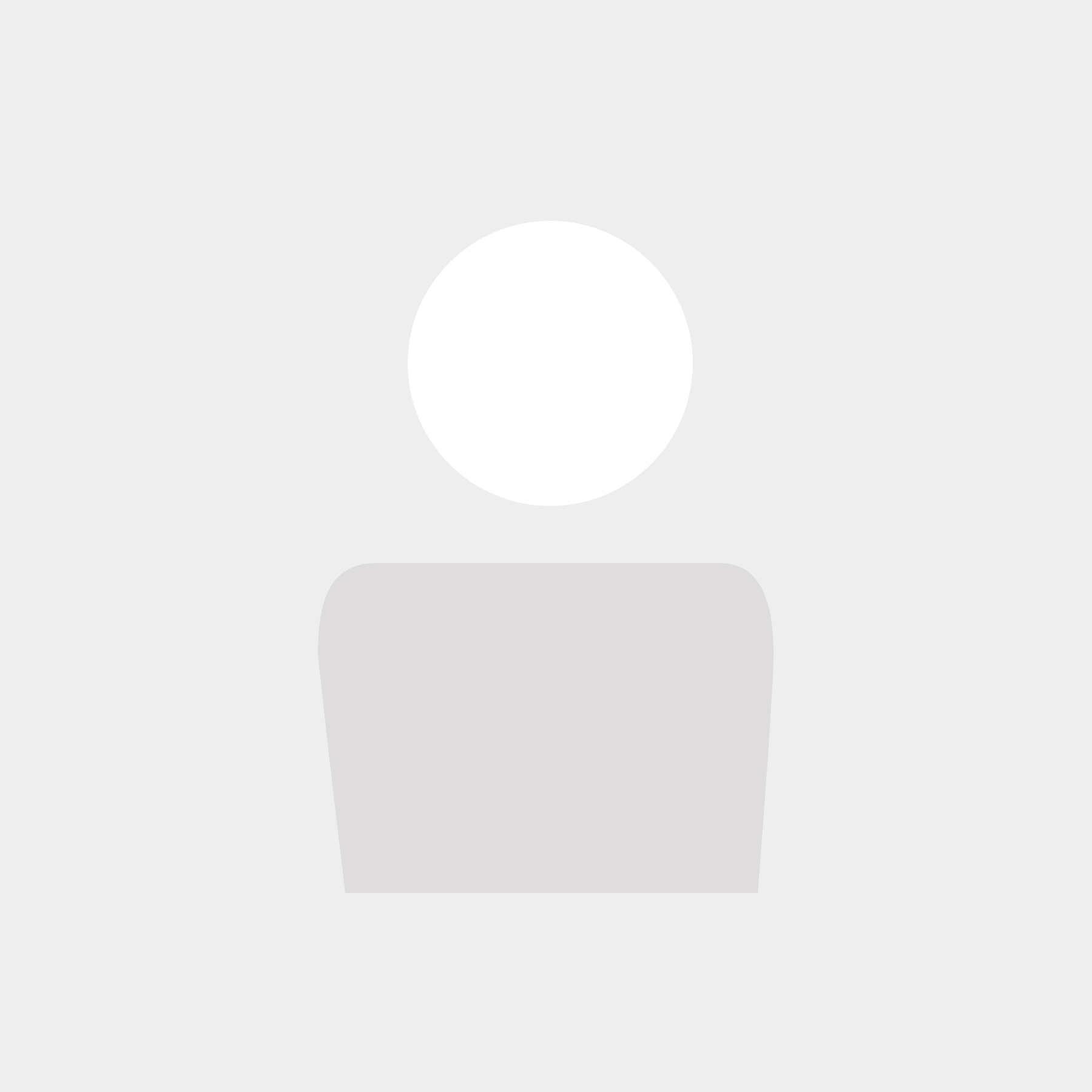
Marcello Fava
Sales
Project Manager
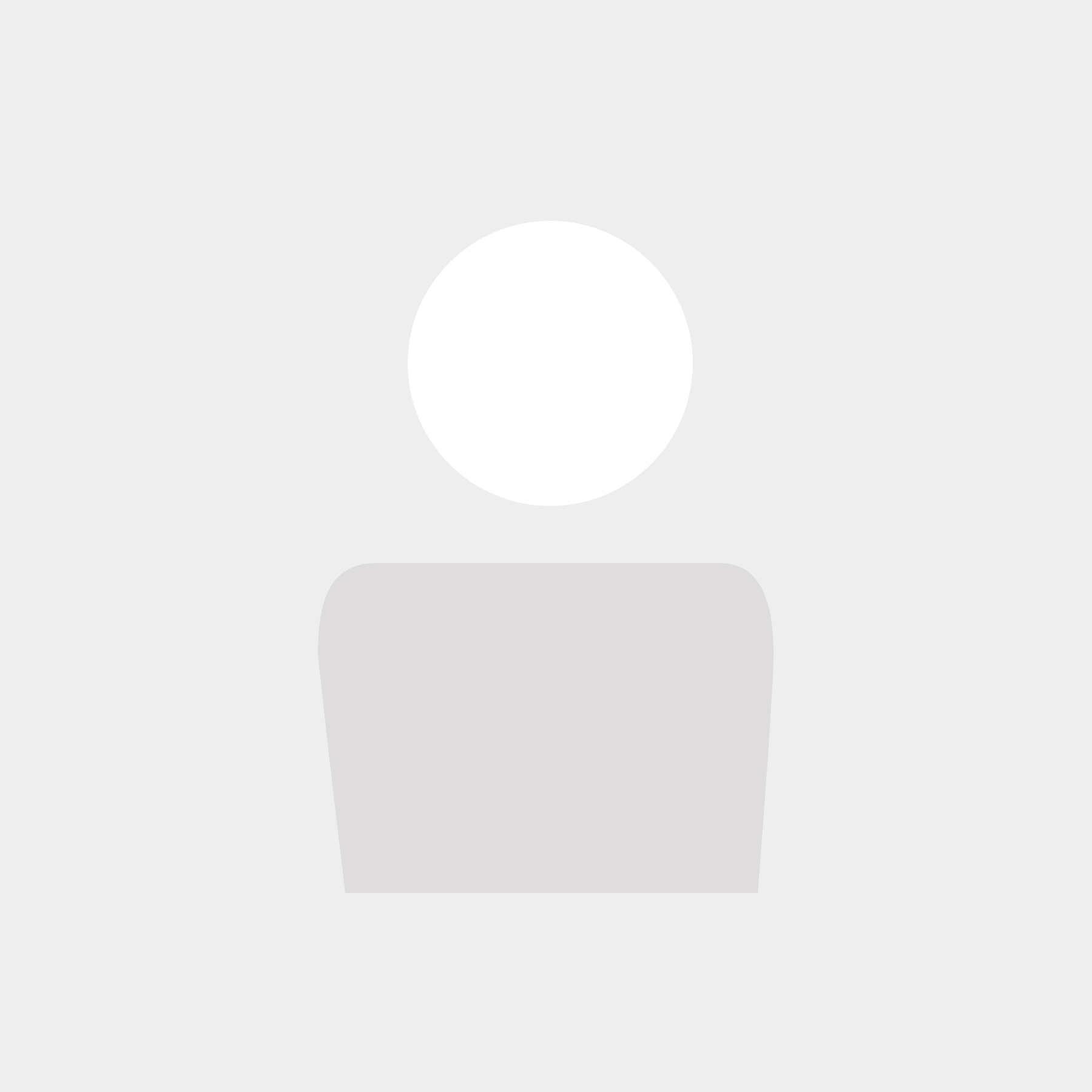
Antonio Fava
Engineering/Design
CEO
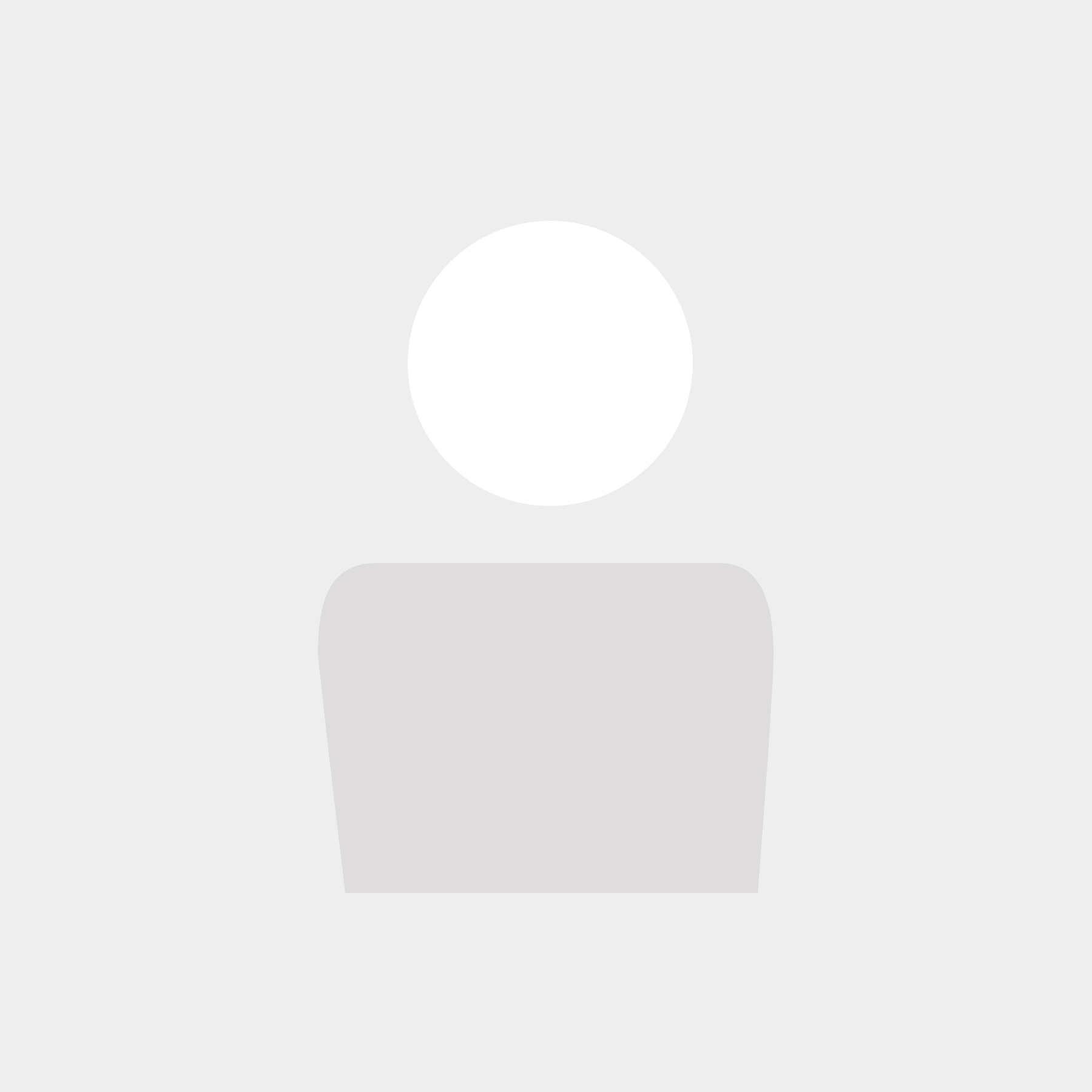