International search engine for Technology for Meat and Alternative Proteins
Status: Exhibitors of IFFA 2025
Coperion GmbH
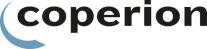
Discover more from us
About us
Reliable Process Technology for Plant-Based Proteins and Meat Alternatives
Coperion is an industry leader in extrusion, feeding and weighing, bulk material handling and service, bringing a wealth of know-how and experience to the plant-based protein and meat alternatives market. As a global mechanical engineering company with more than 140 years of experiences in the field of process technology we develop systems with the requirements of the food industry and end consumers in mind. Our product portfolio comprises:
- High-performance twin screw extruders for all sorts of food applications
- The widest range of feeding solutions in the industry (also see Coperion K-Tron)
- Raw material handling and conveying systems (also see Coperion K-Tron)
- Powder handling and pneumatic transfer
- Rotary and diverter valves
Our systems are suitable for all sorts of plant proteins and designed for handling even difficult ingredients. Coperion has vast experiences in both primary meat substitutes which are Texturized Vegetable Proteins (TVP) and High Moisture Meat Analogues (HMMA).
Texturized Vegetable Proteins
Texturized Vegetable Proteins (TVP) are dehydrated pellets, small flakes, or chunks. They contain 10 to 30 percent moisture and must be soaked in water before further processing and consumption. Thanks to its dry structure it is known for its long shelf life under normal ambient conditions.
High Moisture Meat Analogues
High Moisture Meat Analogues (HMMA) have a water content of 50 to 70 percent and have an equivalent texture to meat products. HMMA is the basis for many vegan or vegetarian ready-to-eat dishes.
Hybrid Extruder for Switching Between TVP and HMMA
To provide food manufacturers with more flexibility Coperion has developed an innovative adapter solution which makes it possible to produce TVP and HMMA on the very same ZSK Food Extruder. This design was even recognized with the 3rd place of the Stuttgart Innovation Prize 2021.
Products in Sanitary Designs
Food extruders, high precision material handling, feeders and components from Coperion and Coperion K-Tron can be provided to the highest hygienic standards for easy cleaning and maintenance. Benefit from clever designs, consistent further developments and hygienic options in accordance with EHEDG, FDA, FSMA and/or GFSI other worldwide initiatives, standards and regulations.
Test Centers Around the World
We work with both established food manufacturers and Start-ups who are dedicated to develop new food products or experiment with common or even novel protein sources. Our test centers around the world are the perfect location to identify and test your equipment requirements for your recipes with the help of our skilled food process engineers.
Learn more: www.coperion.com/food
Also visit the page of our co-exhibitor Coperion K-Tron.
Downloads
Keywords
- Process Technology, Prozesstechnologie
- Extrusion Technology, Extrusionstechnologie
- Food Extruder, Lebensmittelextruder
- Machines for Processing and Production of Plant-Based Proteins and Meat Alternatives, Anlagen zur Bearbeitung und Herstellung von pflanzenbasierten Proteininen und Fleischalternativen
- Components, Rotary Valves, Diverter Valves, Komponenten, Zellenradschleusen, Weichen
Our Products
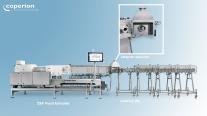
ZSK Food Extruder in Hybrid Design for Production of Plant-Based Meat Alternatives
Coperion’s versatile extrusion technology allows for the production of products with meat-like structure resulting in flavor and texture profiles similar to chicken, pork, beef, and even fish. ZSK food extruders from Coperion ensure maximum throughput and best quality due to high screw speed. The closely intermeshing screws with their tight self-wiping profile eliminate stagnant zones over the whole length of the process section for an optimal mixing behavior. Moreover, the production parameters can be reliably scaled up to other machine sizes. Therefore, the results achieved on a laboratory extruder can be reliably replicated on a production scale.
To provide manufacturers of plant-based products with maximum flexibility Coperion offers a food extruder in hybrid design which was recognized with the 3rd place at the Stuttgart Innovation Prize in 2021. This system allows for an easy switch between the production of Texturized Vegetable Proteins (TVP) and High Moisture Meat Analogues (HMMA) and vice versa. While dry textures, such as soy granules, are directly cut by a centric food pelletizer ZGF, products with a higher water content have to pass through a cooling die. There, the mass is forced into a laminar flow while cooling down which eventually creates meat-like structures. This hybrid design is optimal for companies which need to cover a broad variety of products.
Benefits at a glance:
- Maximum throughput and best quality due to high screw speed
- Optimal mixing behavior
- Closely intermeshing screws with their tight self-wiping profile eliminate stagnant zones over the whole length of the process section
- Hygienic product design: open frame, stainless steel
- High operational reliability and durability
- Suitable for the production of alternative meats, cereals, snacks, pet food and treats and more
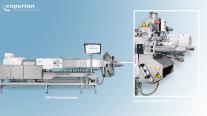
Centric Pelletizer ZGF for the Production of Directly Expanded Food
The ZGF centric pelletizer from Coperion has been used successfully for many years in extrusion plants for the production of directly expanded food stuffs such as cereals, Texturized Vegetable Proteins (TVP), like soy granules or petfood.
The knife rotor of the ZGF centric pelletizer is arranged centrally to the die plate. The product which emerges from the die plate in endless strands is cut off by the knife directly at the end of the extruder (hot die / head pelletizer). The length of the pellets produced can be influenced easily by the number of knives and by the speed of the knife rotor.
The pelletizer hood and the die holder in the ZGF centric pelletizer are swivellable and enable easy access for cleaning the screws, mounting the die plate and quick change over of the die plate. It is connected to the ZSK twin screw extruder by quick release connections.
The knife rotor is spring loaded on the die plate. This ensures a constantly even contact of the knife with the die plate. The distance between the knife blade and the die plate can be finely adjusted during operation. The start-up product in strand or pellet form is discharged through the start-up flap. A safety device ensures that the pelletizer hood does not open until the motor is at a standstill.
Benefits at a glance:
- High product quality due to constantly even contact of the knife with the die plate
- Length of the pellets produced can be influenced easily by the number of knives and by the speed of the knife rotor
- Quick release connections
- Easy access for cleaning the screws, mounting the die plate and quick change over of the die plate
- Safety device ensures that the pelletizer hood does not open until the motor is at a standstill
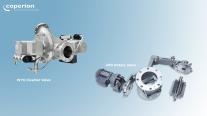
Material Handling Components
Coperion’s material handling components are designed for a wide variety of food applications, including those subject to the most recent hygienic design and cleanability standards. When components must meet the highest hygiene standards, it is advisable to use components with Clean-In-Place (CIP) design, which allow for complete cleaning without removing them from the processing system. For example, Coperion ZRD rotary valves are specially designed for sanitary food applications where contamination is a concern and frequent disassembly and cleaning is required, such as in the processing of allergenic products like soy protein powder. The ZRD rotary valve in hygienic design includes a full access extraction system (FXS) and a large inlet for high filling efficiency. Without removing the valve from the system, the ZRD hygienic can be easily disassembled, cleaned and reassembled. This saves time when switching between products in the manufacturing process. The FXS also fully supports the rotor as it is removed for cleaning, making it an ideal method for facilitating endplate and rotor removal. At the same time, the expanded inlet design ensures high capacities with minimal bridging which is critical when dealing with poor flowing powders. Additionally, Coperion offers a variety of system and component options which are designed to address poor flowing products. A perfect example of this is the new Smart Glide Finish (SGF) anti-stick surface treatment option for Coperion’s rotary valves, which prevents sticking and glazing of ingredients on valve surfaces.
Main features of the ZRD Rotary Valve:
- Pressure range: 1.5 barg (21 psi) system and differential pressure
- Pressure surge proof: 10 barg (145 psi), due to heavy duty design
- ATEX (optional): Usable in EX-Zones and as protection system (flameproof for dust ST2)
- Large inlet / outlet: Without restriction of the cross section for highest capacities
- Outboard bearings: Separated from product by purged seal arrangement and drop out opening
Apart from rotary valves Coperion also specializes in diverter valves which direct material from one source to multiple destinations while making sure that the conveying air and product are forwarded with low resistance. One of our most popular valves in the food industry is the WYK as it meets the highest requirements in regard to hygiene and is available in a CIP-version. As a result, it can also be installed in areas that are difficult to access. The WYK diverter valve is based on an innovative functional principle: During bulk material conveying, the conical rotating body in the conveying position seals the conveying paths from each other. During CIP cleaning, the rotating body is slightly pulled out of the housing and flushed by the cleaning liquid. The conveying tube seal of the WYK is designed in such a way that it also allows the processing of the finest powders. Further advantages are the compact design of the diverter and the high surface quality. All materials used in this valve comply with the EU1935/2004 food regulations and are FDA-compliant.
Main features of WYK Diverter Valve:
- Pressure range: 5 barg (73 psi) system and differential pressure
- Operation Temperature: -20°C up to 100°C
- Seal Configuration: Elastomer seal, tight clearances between rotor and housing
- Material of Construction: Stainless steel
- Surface: Product wetted parts Ra = 0,8 µm
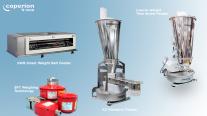
Coperion K-Tron Feeding Systems
Coperion K-Tron offers the widest range of feeding solutions in the industry and a variety of configurations, which can be combined to create an optimal solution for any application. This includes screw feeders, vibratory feeders, bulk solids pumps, weigh belts, liquid feeders and flow meters. Highly accurate gravimetric feeders are particularly helpful when feeding difficult bulk materials, such as plant protein powders used in the production of alternative meats. Thanks to a weight signal, they measure exactly how much bulk material is being fed into the process and as a result they can quickly react to fluctuations in mass flow caused by changes in bulk density or flow disturbances; in addition, their feeding performance is precisely documented.
Liquid feeders use the principle of loss-in-weight measurement. A liquid tank mounted on a weigh scale measures the mass flow of an ingredient into the process. Liquid materials are usually transferred into the extruder using a pump with a variable speed drive. A controller changes the pump speed or stroke to adjust the fluid flow rate to match the setpoint. Highly reliable feeding and refill systems prevent feeding inaccuracies that could cause shutdown of the entire extrusion line which, in turn, adds to process time and calls for cleaning.
Vibratory feeders are ideal where uniform discharge of very free flowing bulk materials is critical, especially at very low rates. A vibratory drive gently moves the bulk material down the feed tray to the discharge. The Coperion K-Tron K3 line of vibratory feeders features improved high accuracy thanks to innovative patent-pending drive technology. The K3 vibratory feeders have a modular design and are available in both standard and hygienic easy clean execution. Vibratory feeders are ideal for gentle handling of a wide range of bulk solid materials, especially fragile ingredients and problem materials such as finished friable food products and ingredients, flakes and fibers.
Benefits at a glance:
- Wide range of feeding tools
- Dependable volumetric feeders
- Highly accurate gravimetric feeders
- State-of-the-art SFT weighing technology
- Advanced controls
- Special food grade finish available for hygienic applications
For more information on Coperion K-Tron and additional process equipment visit the page of our co-exhibitor Coperion K-Tron.